Basic Info.
Model NO.
A48Y
Structure
Spring
Material
Stainless Steel,Carbon Steel,Iron,Brass,Brozen
Type
Spring Type
Materials
Casting, Cast Steel
Fuction
Pressure Relief
Transport Package
Wooden Case
Specification
CE, ROHS, SGS, GMP
Trademark
U-ideal
Origin
Tianjin, China
HS Code
8481804090
Production Capacity
50000PCS/Year
Product Description
A48YSafety Shutoff Valve,Safety Gas Valve
This valve is used for power plant boilers, pressure containers, pressure and temperature reducing devices and other facilities. It serves to ensure the safety of the device during
Structure briefing
1. The main characteristics of the spring fully bore type safety
Valve are: Simple structure, good seal performance, accurate opening pressure, large discharge capability, low differential reseating pressure and convenient adjustment, etc.
2. Nozzle type seat: It is the Laware nozzle type seat. The speed of the steam reaches the velocity of sound when passing the exit way of the seatl; The sealed surface of the seat at is made of hard alloy of cobalt by overlaying welding. Large discharge coefficient, fine abilites of anti friction and corrosion resistance and long durability are recognzed.
3. Thermo elastic disc: The disc is of thermo dlastic sturcture. Taking the advantage of its minor out-of shape feat-Ure when under the medium pressure, the seal ability has been raised, and the problem that pre-discharge phenomenon of the safety valve happens when the medium pressure approaching the set pressure has been overcome. The sealed surface of the disc has adopted the advanced techology of laser heat hardening to increase the hardness and the ability of anti-friction and corrosion sistance.
4. Upper adjusting ring: The valve can acquire appropriate reseating pressure by adjusting the upper adjusting ring to change the flow direc-tion of the medium discharged from the seat.
5. Lower adjusting ring: The valve can rapidly reach full bore in the discharging process by adjusting the adjusting ring.
6. Back pressure adjusting sleeve: It is an auxiliary apparatus that serves to adjust the back pressure of the disc to acquire
Appropriate dif-ferential reseating pressure. P0
Installation instruction
1. The safety valve shall be installed vertically and it would be
Better to install the valve directly upon the adaptor of the container or the pipe. The inside diameter of the adaptor shall be no less than that of the inlet pipe of the safety valve.
2. To avoid the thermal stress that is caused by the thermal expan- sion of the discharge pipe, the exit way of the safety valve shall be equipped with appropriate expansion joint. The inside diameter of the dis-charge pipe should larger than the diameter of the exit way of the valve. Its length shall be as short as possible and no bent isallowed. The weight of both the discharge pipe and the expansion joint shall not be applied to thesafety valve, and they shall be fastened upon the con-struction. The distance between both centerlines of the discharge pipe and the valve body shall be as short as possible.
3. The exit way of the muffler shall have enough area, in order to avord producing back pressure that would affect the discharge capability of the valve.
4. Water drainage pipes shall be installed at the ends of both the exhaust pipe and the body; The exit of the back pressure adjusting
Sleeve shal be equipped with short bend.

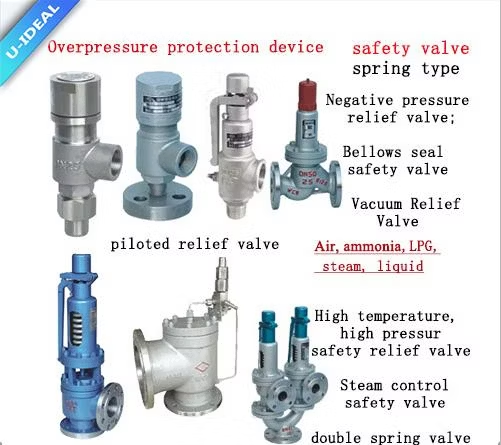

This valve is used for power plant boilers, pressure containers, pressure and temperature reducing devices and other facilities. It serves to ensure the safety of the device during
Structure briefing
1. The main characteristics of the spring fully bore type safety
Valve are: Simple structure, good seal performance, accurate opening pressure, large discharge capability, low differential reseating pressure and convenient adjustment, etc.
2. Nozzle type seat: It is the Laware nozzle type seat. The speed of the steam reaches the velocity of sound when passing the exit way of the seatl; The sealed surface of the seat at is made of hard alloy of cobalt by overlaying welding. Large discharge coefficient, fine abilites of anti friction and corrosion resistance and long durability are recognzed.
3. Thermo elastic disc: The disc is of thermo dlastic sturcture. Taking the advantage of its minor out-of shape feat-Ure when under the medium pressure, the seal ability has been raised, and the problem that pre-discharge phenomenon of the safety valve happens when the medium pressure approaching the set pressure has been overcome. The sealed surface of the disc has adopted the advanced techology of laser heat hardening to increase the hardness and the ability of anti-friction and corrosion sistance.
4. Upper adjusting ring: The valve can acquire appropriate reseating pressure by adjusting the upper adjusting ring to change the flow direc-tion of the medium discharged from the seat.
5. Lower adjusting ring: The valve can rapidly reach full bore in the discharging process by adjusting the adjusting ring.
6. Back pressure adjusting sleeve: It is an auxiliary apparatus that serves to adjust the back pressure of the disc to acquire
Appropriate dif-ferential reseating pressure. P0
Installation instruction
1. The safety valve shall be installed vertically and it would be
Better to install the valve directly upon the adaptor of the container or the pipe. The inside diameter of the adaptor shall be no less than that of the inlet pipe of the safety valve.
2. To avoid the thermal stress that is caused by the thermal expan- sion of the discharge pipe, the exit way of the safety valve shall be equipped with appropriate expansion joint. The inside diameter of the dis-charge pipe should larger than the diameter of the exit way of the valve. Its length shall be as short as possible and no bent isallowed. The weight of both the discharge pipe and the expansion joint shall not be applied to thesafety valve, and they shall be fastened upon the con-struction. The distance between both centerlines of the discharge pipe and the valve body shall be as short as possible.
3. The exit way of the muffler shall have enough area, in order to avord producing back pressure that would affect the discharge capability of the valve.
4. Water drainage pipes shall be installed at the ends of both the exhaust pipe and the body; The exit of the back pressure adjusting
Sleeve shal be equipped with short bend.
Main external and connecting dimensions | |||||||||||
Type | DN Nominal diameter | Dimensions (mm) | |||||||||
L | L 1 | Do | H | DN' | D | D 1 ' | D 2 ' | B' | Z'-d' | ||
A68Y-20 | 65 | 210 | 290 | 48 | 923 | 150 | 300 | 250 | 204 | 30 | 8-25 |
A68Y-P 54 10V | 65 | 210 | 290 | 48 | 923 | 150 | 300 | 250 | 204 | 30 | 8-25 |
A68Y-20 | 80 | 210 | 290 | 52 | 923 | 150 | 300 | 250 | 204 | 30 | 8-25 |
A68Y-P 54 10V | 80 | 210 | 290 | 52 | 923 | 150 | 300 | 250 | 204 | 30 | 8-25 |
A68Y-25 | 65 | 210 | 290 | 48 | 923 | 150 | 300 | 250 | 204 | 30 | 8-25 |
A68Y-P 54 14V | 65 | 210 | 290 | 48 | 923 | 150 | 300 | 250 | 204 | 30 | 8-25 |
A68Y-25 | 80 | 210 | 290 | 52 | 1,003 | 150 | 300 | 250 | 204 | 30 | 8-25 |
A68Y-P 54 14V | 80 | 210 | 290 | 52 | 1,003 | 150 | 300 | 250 | 204 | 30 | 8-25 |
A68Y-32 | 65 | 210 | 290 | 48 | 1,083 | 150 | 300 | 250 | 204 | 30 | 8-25 |
A68Y-P 54 20V | 65 | 210 | 290 | 48 | 1,083 | 150 | 300 | 250 | 204 | 30 | 8-25 |
A68Y-32 | 80 | 210 | 290 | 52 | 1,083 | 150 | 300 | 250 | 204 | 30 | 8-25 |
A68Y-P 54 20V | 80 | 210 | 290 | 52 | 1,083 | 150 | 300 | 250 | 204 | 30 | 8-25 |
A68Y-10 | 150 | 310 | 525 | 100 | 1,158 | 300 | 485 | 430 | 390 | 36 | 16-30 |
A68Y-P 54 3.82V | 150 | 310 | 525 | 100 | 1,158 | 300 | 485 | 430 | 390 | 36 | 16-30 |
A68Y-10 | 200 | 310 | 525 | 125 | 1,158 | 300 | 485 | 430 | 390 | 36 | 16-30 |
A68Y-P 54 2.5V | 200 | 310 | 525 | 125 | 1,158 | 300 | 485 | 430 | 390 | 36 | 16-30 |

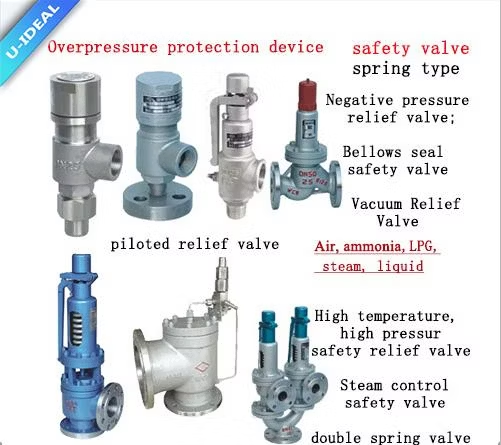

